When the casting is over, we sort bullets. Not every bullet you cast is suitable and each bullet caster sets up his/her own quality control system. Your bullets are as good as you make them, and sorting bullets is an immediate visual quality control check.
I cast a bunch of bullets tonight for my .30-30. The bullets are the well-known Lyman 311041. Lyman has been making molds for this bullet for years. It is a flat point, 170 grain .30 caliber bullet and has a history of good accuracy in the .30-30. These particular bullets came out of custom Lee 6-cavity mold that a group of us ordered through the Cast Boolits forum. Tonight was my first time to try this mold (or any 6-cavity mold) and it makes a pile of bullets quickly. Very quickly.
I pulled four of them out of the pile for illustation purposes.
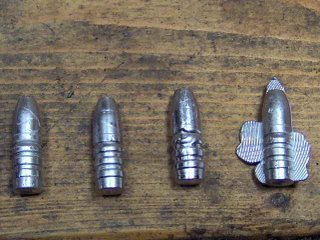
Lets look at them, left to right.
The far left bullet is frosted and has a small wrinkle on the nose. Frosting is indicative of a mold that is too hot, or alloy that is too hot. This particular bullet came at the end of the production run and my pot tends to let the metal get a little hot at the end of the run. Frosted bullets are okay with me, as I think that the lubricant tends to adhere to them better than a shiny bullet. The wrinkle isn't really a reason to reject the bullet because it is very shallow. This bullet goes in the initial keeper pile.
The second bullet is nearly perfect in every way. It is well filled out with well-defined bands. This bullet is what we are looking for and it, likewise, goes in the keeper pile. A substantial majority of the bullets I cast tonight look just like this.
The third bullet shows signs of a cold mold. It isn't well filled out, the bands are not well defined, and it has a void that appears as a wrinkle on the topmost band. It probably came from the initial few bullets in the production run and it will be rejected. It won't be wasted, though, because I'll melt it down next time and try again.
The fourth, the far right bullet, shows a defect that we call flashing. The mold wasn't closed properly and the lead ran between the mold-halves. When you see flashing, stop immediately and find the culprit. In this case, a small piece of trash had gotten between the mold halves and I brushed it out with the tip of a screwdriver. This bullet will also go in the reject pile and will be melted the next time I heat up the pot.
I normally reject about twenty percent of the bullets I cast during the first, visual sorting. For one reason or another, a bullet might not make the cut, and goes in the reject pile. When I cast bullets for hunting, I sort them by weight and keep bullets that fall into a fairly narrow weight range. If I were sorting for a match, I would sort those bullets that were absolutely perfect, both visually and by weight. The remaining bullets would go into another pile, for plinking or informal practice.
The next step, when the pile of bullets cools, is to sort them again visually in case I missed one that needs to go into the reject pile. Then I lube them, size them and seat gas checks. After that, they are ready for loading.
Thanks for the input Dennis. I feel better knowing I'm not the onl one with a 1 in 5 reject rate! But casting has been good and the folks at castboolits have treated me well. Thanks Jerry
ReplyDelete